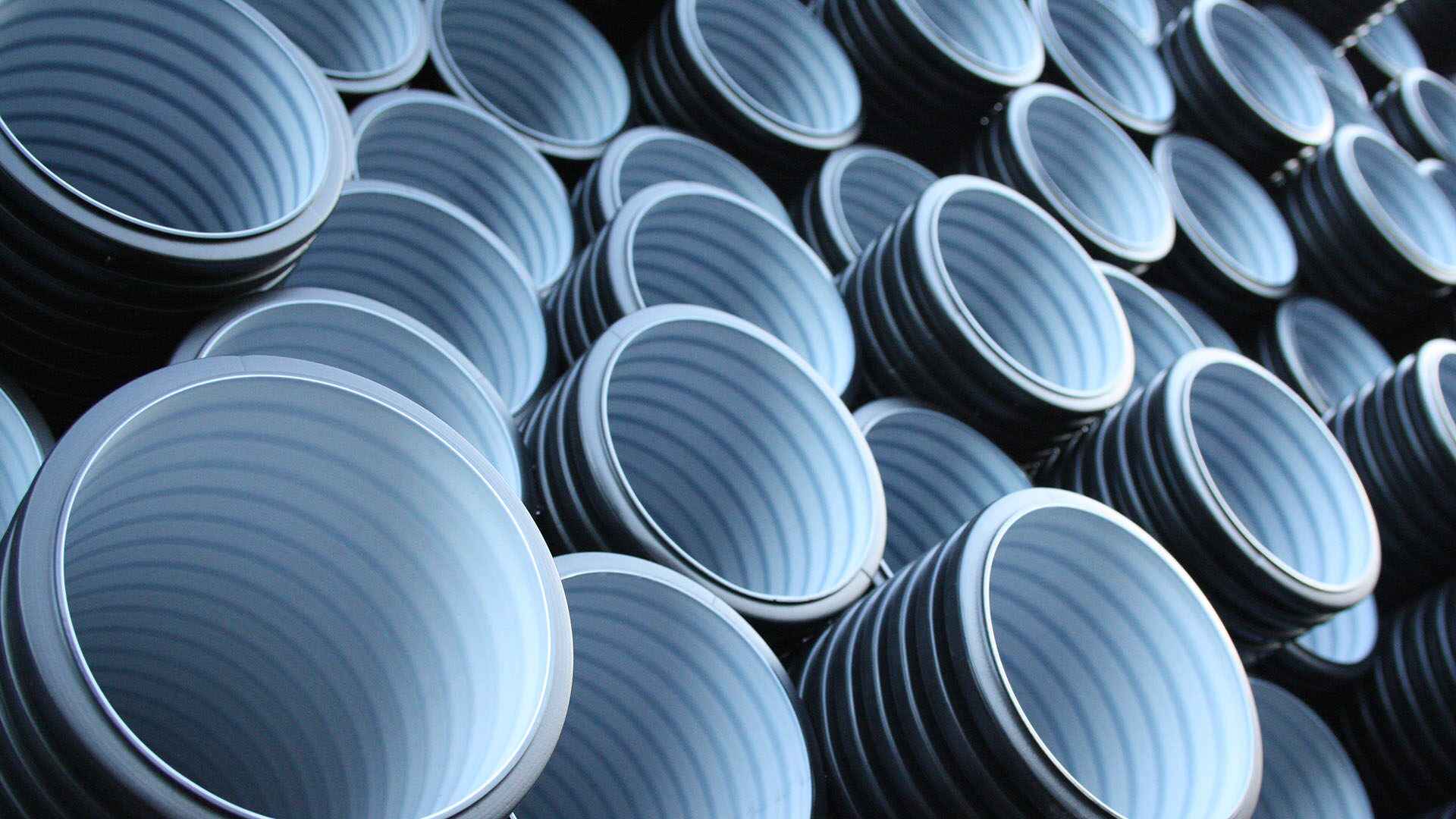
HDPE pipes in construction are revolutionizing the way we build infrastructure. As urban growth accelerates and sustainability becomes a priority, high-density polyethylene (HDPE) pipes offer a flexible, reliable, and environmentally conscious alternative to traditional materials.
What Are HDPE Pipes and Why Are They Popular in Construction?
HDPE (High-Density Polyethylene) is a thermoplastic known for its strength and versatility. It resists corrosion, handles pressure, and adapts well to different environments.
Read how HDPE compares to other materials like carbon steel and stainless steel
Main Advantages of HDPE Pipes in Construction
1. Excellent Corrosion Resistance
HDPE does not rust or degrade due to chemicals or soil conditions. This reduces the risk of pipe failure and saves on maintenance costs.
2. Flexibility and Ductility
Highly flexible, HDPE bends around obstacles and absorbs ground movement. Ideal for earthquake-prone areas and rough terrain.
3. Lightweight and Easy to Install
HDPE pipes are much lighter than steel or concrete, requiring less labor and machinery, which lowers installation costs.
4. Leak-Proof Joints
Using electro-fusion or butt fusion joints, HDPE systems are nearly leak-free, boosting system efficiency and reducing water loss.
5. Long-Term Cost Savings
HDPE offers durability and low maintenance, often lasting over 50 years, making it cost-effective throughout its lifecycle.
6. Eco-Friendly and Sustainable
HDPE is recyclable and lightweight, which minimizes carbon emissions during transport and installation—key for Scandinavian eco-regulations.
Applications of HDPE Pipes in Construction
- Water distribution systems
- Sewage and drainage networks
- Natural gas pipelines
- Agricultural irrigation
- Telecommunication ducting
Why HDPE Pipes Matter in the Scandinavian Context
- Effective in freeze-thaw cycles
- Performs well in shifting soil and cold climates
- Supports EU-wide sustainability goals
- Preferred material in eco-certified construction
HDPE vs Iron Pipes – Quick Comparison
Feature | HDPE Pipes | Iron Pipes |
---|---|---|
Corrosion Resistance | Excellent | Poor |
Installation | Quick and low-labor | Labor-intensive |
Environmental Impact | Recyclable, low emissions | High carbon footprint |
Cost Over Time | Low | High |
Conclusion: Building Smarter with HDPE Pipes
HDPE pipes in construction offer unmatched flexibility, durability, and sustainability. Especially in the Nordic region, where weather extremes and environmental standards are strict, HDPE pipes provide a future-proof solution. For reliable, eco-conscious infrastructure, HDPE is the way forward.
Explore more: