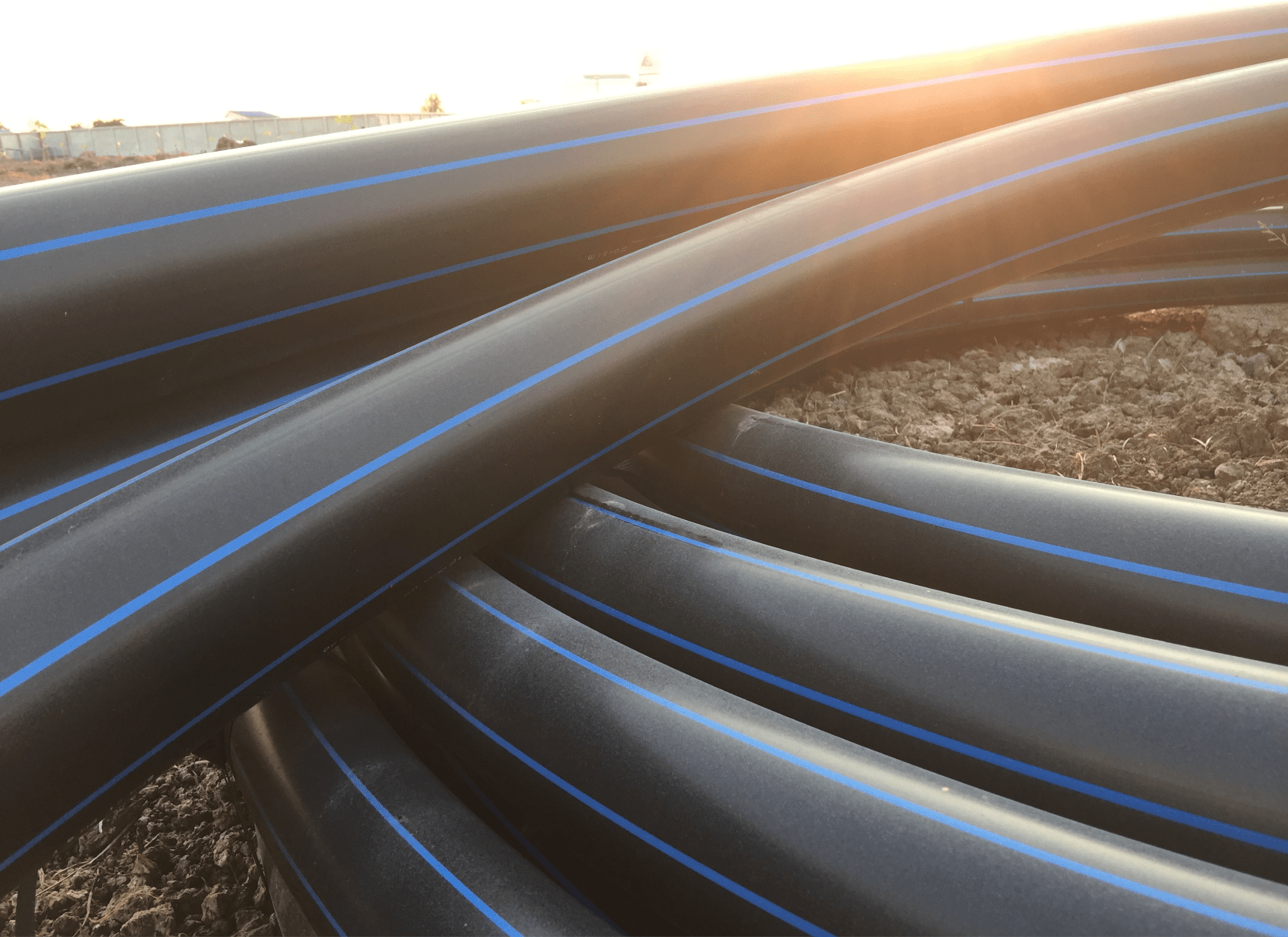
Energy-efficient piping solutions are increasingly vital in modern construction and industrial systems, from residential buildings to large-scale infrastructure projects. With growing emphasis on sustainability and reduced operational costs, choosing the right pipe material—HDPE, carbon steel, or stainless steel—can significantly impact long-term energy savings across Scandinavia and beyond.
Energy Savings in Piping Systems
Energy use in piping systems is significantly influenced by several factors. An understanding of these will assist in selecting the most energy-efficient piping material:
- Friction Loss: The friction between the fluid in flow and the inner wall surface of the pipe as it advances through the pipes produces friction losses. This friction causes the resistance that, consequently, leads to the fall in pressure in the direction of travel along the pipe. Combating this pressure drop entails higher energy consumption by the action of pumps to sustain a good flow rate.
- Scaling and Corrosion:
- Scaling: The deposition of mineral scaling on the inside walls of the pipe greatly increases the friction. The deposit reduces the effective diameter of the pipe interior through which the fluid is flowing, therefore creating a blockage to flow and increasing the energy required for a given flow rate.
- Corrosion: Internal surface erosion, especially in the case of metal pipes, is caused by corrosion. It leads to increased roughness, which further causes increased friction losses.
- Heat Loss: In heating and cooling systems, the material of the pipe is very significant in the matter of heat transfer.
HDPE Pipes: Energy-Saving Advantages
HDPE pipes have a number of key advantages that contribute to significant energy savings:
By carefully considering these factors and selecting piping materials that minimize friction, resist corrosion and scaling, and optimize heat transfer, it’s possible to significantly improve the energy efficiency of any piping system.
Carbon Steel Pipes: Energy-Saving Considerations
Though very common, carbon steel poses some problems as far as energy efficiency is concerned.
- Corrosion and Scaling:
- Carbon steel can easily corrode, particularly if the surrounding environment contains moisture and oxygen. The product is rust, which increases the friction in the pipe immensely.
- The problem is accentuated by scaling or mineral deposits on the inner walls of the pipe.
- Both corrosion and scaling decrease the effective diameter of the pipe, increasing fluid resistance and hence requiring increased consumption of energy by pumps in maintaining flow.
- These increased energy requirements, however, mean increased operation costs, besides shorter lifetimes, which both involve high financial investments in either repairs or complete replacements.
- Heat Loss:
- Carbon steel is a good conductor of heat. As a result, there are huge losses in the transportation of heat through the walls of such pipes in heating and cooling systems.
- In heating systems, the heat could easily be lost to the surrounding environment, reducing efficiency and increasing energy consumption to maintain certain temperatures.
- Whereas in cooling systems, the system can pick up heat from the surroundings and reduce efficiency in the cooling of the system.
- Energy-Efficient Coatings:
- In order to enhance these effects of corrosion and heat loss, the carbon steel pipes are normally coated with a number of materials, including:
- Insulation: These insulation materials mainly include fiberglass and foam; they greatly reduce heat loss and, therefore, improve efficiency in heating and cooling systems.
- Protective Coatings: Coatings of paint, epoxy, or zinc protect against corrosion and, as such, elongate the life of the pipe, hence minimizing the frequency of replacement and the use of energy in re-replacement.
- In order to enhance these effects of corrosion and heat loss, the carbon steel pipes are normally coated with a number of materials, including:
This would go a long way to reduce the environmental effects of carbon steel piping systems through better energy efficiency. Necessary corrosion protection and effective insulation of carbon steel piping systems are provided.
Stainless Steel Pipes: Energy-Saving Advantages
Some of the important characteristics related to saving energy in such pipes include the following:
- Excellent Corrosion Resistance: Stainless steel is extremely resistant to the attack of corrosion, hence very minimum chances of scaling or building up in any pipe. This therefore greatly reduces friction losses and hence pressure drops and energy use by pumps. The inner surface of the stainless steel pipes is very smooth, ensuring that fluids can flow nicely with minimum resistance, thus reducing the need to put more power into pumping. This results in reduced energy consumption, hence lower operating costs in the long run.
- Extreme Strength and Durability: Resilience, strength and durability come as stainless steel features allowing for the use of thinner pipe walls for maintaining structural integrity. Reduced material usage translates to the following:
- Energy consumption gets reduced during manufacturing: Less material requires less energy to extract, process, and transport.
- Reduced environmental impact: Lower material usage minimizes the environmental impact associated with material extraction and processing.
By minimizing friction losses, maximizing energy efficiency, and reducing material usage, stainless steel pipes help conserve a lot of energy over their life cycle.
HDPE vs Carbon Steel vs Stainless Steel: A Comparative Analysis
There is a comparison table showing some of the major differences in HDPE, carbon steel, and stainless steel pipes based on the parameters below.
Feature | HDPE Pipes | Carbon Steel Pipes | Stainless Steel Pipes |
---|---|---|---|
Friction Loss | Very Low – Smooth inner surface minimizes friction | Moderate to High – Susceptible to corrosion and scaling, increasing friction | Low – Smooth inner surface and corrosion resistance minimize friction |
Corrosion Resistance | Excellent – Inherently resistant to corrosion | Poor – Prone to corrosion and rust, requiring protective coatings | Excellent – Highly resistant to corrosion |
Heat Loss | Low – Good insulator, minimizing heat transfer | High – Good conductor of heat, leading to potential heat loss | Moderate – Lower heat conductivity compared to carbon steel |
Maintenance Requirements | Low – Minimal maintenance due to corrosion resistance | High – Requires regular maintenance and potential repairs due to corrosion | Low – Minimal maintenance due to corrosion resistance |
Long-Term Energy Costs | Low – Energy-efficient due to low friction, minimal scaling, and long lifespan | Moderate to High – Potential for increased energy costs due to corrosion, scaling, and maintenance needs | Low – Energy-efficient due to low friction, corrosion resistance, and long lifespan |
Selecting the Right Pipe Material for Energy Efficiency
Energy efficiency in the selection of the right piping material is primarily determined by application, type of fluid transported, operating temperature, or higher applied pressure ratings.
- Application: The specific application will tell the necessary properties of the piping system. Factors to consider include the type of fluid being transported, the operating temperature, and the required pressure rating.
- Fluid Type: The type of material selected is dependent on the choice of fluid that passes through it. Many will have corrosive properties; most will have temperature and pressure ratings different to ensure conduction.
- Temperature: Operating temperature is very crucial to the system. Some materials may be sensitive to temperature resistance limits, thus affecting energy efficiency and overall performance throughout the system’s lifetime.
- Pressure: The pressure rating in the pipe should be suitable for the application. Higher pressure requirements and applications may require thicker walls or stronger materials.
- Budget: The big initial cost of the pipe material i.e. the main factor the budget. In contrast, initial costs had to be weighed against the long-term energy savings and maintenance costs.
- Environmental Impact: The various environmental impacts produced by these materials have to be scrutinized, manufacturing processes taken into consideration, recyclable, and also the actual or potential emissions or contamination.
Lifecycle Cost Analysis:
No decision can be made without doing the LCCA. LCCA considers the overall cost of ownership during the lifetime of the piping system:
- Initial Costs: Material, manufacturing, and installation costs.
- Operating Costs: The energy consumption in pumping, heating, or cooling.
- Maintenance Costs: Repair and replacement costs and costs associated with protection against corrosion.
- Environmental Costs: The environmental impact due to material production, utilization, and disposal.
By doing an LCCA, you will know how the various options for pipe material compare in the long term with regard to cost, energy usage, and efficiencies and therefore which will serve the needs of your project with efficiency and value.
Potential Challenges and Considerations
While all of the materials listed above present multiple significant advantages, particular problems are impossible to fully preclude:
- HDPE:
- Temperature Limitations: HDPE has some definite temperature limitations. Very high temperatures for a longer period of time may soften the pipe and possibly cause it to deform. On the other side, extremely low temperatures will increase the possibility of embrittlement and the development of cracks.
- UV Degradation: HDPE may degrade from long-term direct sunlight and UV exposure. It will embrittle the material and shorten the service life.
- Carbon Steel:
- Corrosion and Scaling: Carbon steel is highly prone to corrosion, thus giving rise to rust and scaling. This increases friction very significantly, hence restricting the flow of fluids and requiring more maintenance, including the following:
- Corrosion Protection: Painting or applying zinc coatings for protection against corrosion.
- Regular Inspections: In terms of repairs, more frequent inspections and even expensive repairs due to corrosion damage.
- Stainless Steel:
- Higher Upfront Cost: Compared to HDPE and carbon steel, the initial cost of stainless steel is often higher.
- The higher initial cost must be balanced very carefully against the long-term compounding benefits of corrosion resistance and reduced maintenance.
- Higher Upfront Cost: Compared to HDPE and carbon steel, the initial cost of stainless steel is often higher.
- Corrosion and Scaling: Carbon steel is highly prone to corrosion, thus giving rise to rust and scaling. This increases friction very significantly, hence restricting the flow of fluids and requiring more maintenance, including the following:
Taking into account these potential drawbacks and choosing the right material for the right application and the environment in which it will operate, you can eliminate and mitigate risk while ensuring a long-lasting and energy-efficient piping system.
Environment & Features
- Disadvantages of HDPE Pipe:
- Temperature limits (both high and low)
- Subject to UV degradation if left unprotected
- Vulnerable to many chemicals
- Relatively brittle compared to some metals and prone to severe pressure
- Two Main Advantages of Stainless Steel Pipe Over Carbon Steel Pipe:
- Excellent Corrosion Resistance: Stainless steel resists corrosion primarily better than most carbon steel pipes. Stainless steel reduces the possibility of scaling in the pipe, prolonging the performances with fewer maintenance costs.
- High Strength-to-Weight Ratio: Stainless steel piping has a higher strength-to-weight ratio than carbon steel; therefore, there can be thinner-walled piping and hence retain their strength. It can help to save the amount of raw material required and hence have fewer environmental effects.
- Environmental Friendliness of HDPE Pipe:
- HDPE is a recyclable material; thus, very little goes into the waste management system and hence is more environmentally friendly in the industry.
- Manufacturing Process of HDPE: The manufacturing process for HDPE has relatively lower environmental impact compared with that for some other materials.
- Fuel Resistance of HDPE Pipe:
- HDPE pipes are practically resistant to so many types of fuels that involve gasolene, diesel, and also jet fuel.
- However, in making the pipe suitable for any specific fuel, it is necessary to select the proper grade of HDPE and to take proper installation.
These will also become areas of further research that will help engineers and designers to consider in greater detail various benefits and limitations of these types of piping material in order to make informed decisions relevant to particular projects.
Conclusion
Selection of an appropriate piping material is important in achieving effective energy efficiency for a particular system. There will be great differences among HDPE, carbon steel, or stainless steel on overall energy consumption, frequency of maintenance, and effects on the environment.
- HDPE: Has excellent corrosion resistance, low friction, and is easy to install, which results in huge energy savings. Temperature limitations and possible UV degradations shall be kept in mind.
- Carbon steel: Although it seems inexpensive initially, it will have higher energy consumption due to its susceptibility to corrosion and scaling and thus requires frequent maintenance.
- Stainless steel: It features good corrosion resistance and high strength, with a mainly higher initial cost in terms of low energy losses and minimum maintenance cost.
The selection of appropriate application conditions includes pressures, temperatures, and chemicals to be conveyed, with lifecycle cost consideration of an appropriate decision that could ensure an effective choice for energy-efficient and sustainable piping in each separate application.
In the future, further research and development in material science will surely unlock even more innovative and energy-efficient piping solutions. These developments in this area play a very important role in increasing energy efficiency and sustainability in everything from residential and commercial building projects to major industrial works.
It is highly recommended to consult more experienced engineers and piping specialists in related fields for a more professional selection of piping material suited to one’s own purpose.
Learn more about the advantages of HDPE in construction here or explore how plastic pipes compare to iron systems in performance and longevity.